Understanding Tooling Molds: A Comprehensive Guide for Metal Fabricators
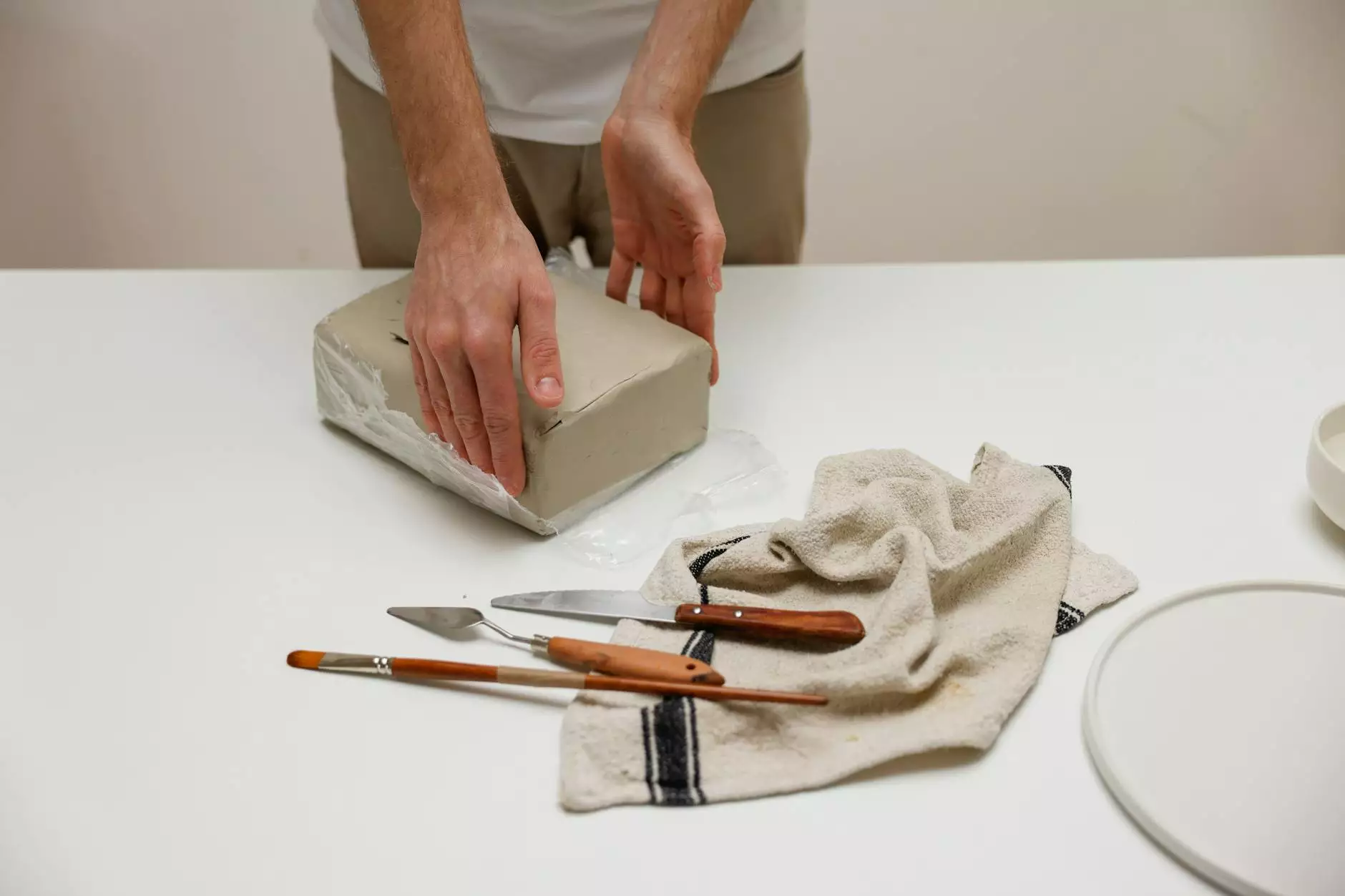
In the ever-evolving landscape of manufacturing, tooling molds play a pivotal role, particularly in the realm of metal fabrication. These molds are not just mere tools; they are the backbone of efficient production, ensuring that components are shaped accurately and consistently. This article aims to provide an in-depth understanding of tooling molds, their applications, and their significance within the metal fabricators industry.
What Are Tooling Molds?
Tooling molds are specialized tools used in the manufacturing process to shape and form materials into precise components. They are often crafted from durable materials such as steel, aluminum, or synthetic materials to withstand the intense pressures and temperatures involved in the manufacturing process. Tooling molds are essential in producing items ranging from simple brackets to complex automotive parts.
Types of Tooling Molds
Understanding the different types of tooling molds is vital for metal fabricators to choose the right mold for their production needs. Here are some common types:
- Injection Molds: Used primarily in plastic manufacturing, these molds inject molten material into a mold cavity to create detailed shapes.
- Die Cast Molds: Commonly used in metal die casting, these molds enable the production of aluminum, zinc, and magnesium components.
- Blow Molds: Primarily used for hollow plastic products, these molds introduce air into liquid plastic to create bottles and containers.
- Compression Molds: Used for thermoplastic and thermoset materials, these molds compress the material into a desired shape.
- Extrusion Molds: These molds are used to create long shapes like pipes and tubing through a continuous process.
The Significance of Tooling Molds in Metal Fabrication
Tooling molds are essential to the metal fabrication process for several reasons:
1. Precision and Consistency
The most significant advantage of using tooling molds is the precision they offer. In industries where every millimeter counts, molds ensure that components are produced with exact measurements consistently. This consistency is crucial for ensuring the final product meets strict quality standards.
2. Enhanced Efficiency
Using molds accelerates production rates significantly. By utilizing tooling molds, metal fabricators can produce large volumes of parts in a fraction of the time it would take using other manufacturing methods. This efficiency not only saves time but also enhances overall operating profitability.
3. Cost-Effective Production
While the initial investment in tooling molds can be significant, the long-term savings are undeniable. Molds reduce material waste and labor costs, contributing to a lower cost per part. As production ramps up, these cost savings translate into increased profit margins.
4. Flexibility and Customization
With modernization, tooling molds can be customized to accommodate various designs and specifications. This allows fabricators to adapt to changing market demands and offers customers a level of customization that enhances product appeal.
Materials Used in Tooling Molds
The material used for tooling molds is crucial as it directly impacts the mold’s durability and production quality. Here is a look at the commonly used materials:
- Steel: Known for its strength and longevity, steel is commonly used for making tooling molds for metal fabrication.
- Aluminum: Lightweight and easy to machine, aluminum molds are ideal for lower-volume projects and prototyping.
- Polymeric materials: In some applications, advanced polymers provide a cost-effective and lightweight alternative for specific mold types.
The Process of Creating Tooling Molds
Creating effective tooling molds involves several steps:
1. Design Phase
The process begins with the design phase, where engineers create 3D models of the mold using CAD (Computer-Aided Design) software. This initial design will dictate the mold’s functionality and performance.
2. Material Selection
Depending on the production needs, the appropriate materials are selected based on durability, thermal resistance, and cost considerations.
3. Machining the Mold
Once the design and materials are finalized, the machining process begins. CNC (Computer Numerical Control) machines are often used for precise crafting. This phase is critical in ensuring that mold components fit together perfectly.
4. Mold Assembly
After machining, the various components of the mold are assembled. This stage may include several alignments and tests to ensure everything fits correctly.
5. Testing and Refining
Molds undergo rigorous testing to check for imperfections and efficiency. Any necessary refinements are made to enhance performance.
The Role of Tooling Molds in Product Development
In the product development life cycle, tooling molds play an integral role, allowing engineers to produce prototypes for testing and further refinement. The rapid prototyping process enables manufacturers to evaluate designs quickly, ensuring that the final products meet market expectations.
Importance in Rapid Prototyping
Rapid prototyping with tooling molds accelerates the product development cycle. It helps identify design flaws early, leading to improved product quality and better market-readiness.
Future Trends in Tooling Molds
The landscape for tooling molds continues to evolve, influenced by advancements in technology and changes in market demands. Here are some emerging trends:
- 3D Printing: Innovations in 3D printing technologies are paving the way for new types of molds that are more flexible and customizable than ever before.
- Smart Molds: Incorporating IoT (Internet of Things) technology into molds allows for real-time monitoring and performance analytics, increasing efficiency and quality.
- Environmentally-Friendly Materials: Sustainable materials are being used in mold production, aligning with global sustainability goals and reducing the carbon footprint.
Challenges Faced by Metal Fabricators in Tooling Molds
Despite the numerous advantages, metal fabricators face challenges when it comes to the use of tooling molds:
1. High Initial Investment
The cost of designing and producing custom molds can be significant. This financial barrier can be a challenge for smaller fabricators, although the long-term savings usually justify the investment.
2. Maintenance Requirements
Proper maintenance of molds is crucial to prolong their lifespan. Fabricators must dedicate resources toward ongoing mold maintenance to avoid production delays caused by mold failure.
3. Limitations in Design Flexibility
Once a mold is created, making changes can be a time-consuming and costly process. This inflexibility can limit a fabricator's ability to adapt designs quickly to market changes.
Conclusion
In summary, tooling molds are an indispensable part of the metal fabrication industry. They provide the precision, efficiency, and cost-effectiveness needed to meet today's manufacturing demands. As technology advances and new materials emerge, the future of tooling molds promises even greater innovations, enabling metal fabricators to enhance their production capabilities. For businesses in the industry, investing in high-quality molds is not just a choice, but a necessity for maintaining a competitive edge in the market.
For more information about tooling molds and their impact on metal fabrication, visit deepmould.net.